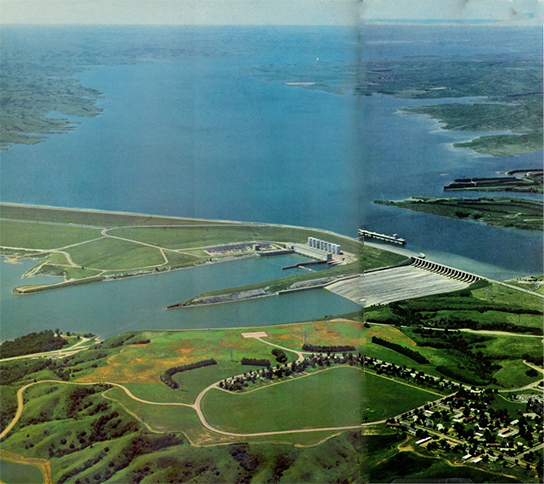 |
Fort Randall Dam, 11 July 1967 - Graphic restoration by Al Barrus
|
Fort Randall Dam was the first Pick-Sloan dam completed by the Omaha District. Located in South Dakota just north of the Nebraska line, the dam was named for a nearby Indian war fort, of which only a ruined chapel, an overgrown parade ground, and a collection of debris-filled cellars remained. From 1946 to 1948, the Omaha District planned and designed a 160-foot-high, 28-million-cubic-yard, rolledfill, earthen dam to tame the Missouri at Fort Randall and to produce some 320,000 kilowatts of hydroelectric power.
In order to build the dam and the 150-mile-long reservoir it would impound, the Corps first had to provide access to the site for men, machines, and materials. Lake Andes, South Dakota, located about 8 miles from the damsite, was the nearest town with rail and highway connections. Corps workmen built a railroad to the damsite from the Chicago, Milwaukee, St. Paul, and Pacific tracks at Lake Andes. During the 6 years the spur was used, it carried 38,425 railcars to the dam. The Omaha District also built an access road to the site. The Corps invested more than $1.4 million in the rail spur and access road alone.
Like Fort Peck and Garrison Dams, Fort Randall Dam required a new town to house the people who would build and maintain it. During the years from 1946 to 1950, the Omaha District built Pickstown, South Dakota, on a bluff east of the river at a cost of $9.5 million. It constructed 18 dormitories, 312 family dwellings, 25 utility buildings servicing 625 trailer spaces, 3 cafeterias, a school building, a theater, a hospital, and a hotel. The town was designed to house 3,500 workers in conditions suitable for normal family life.
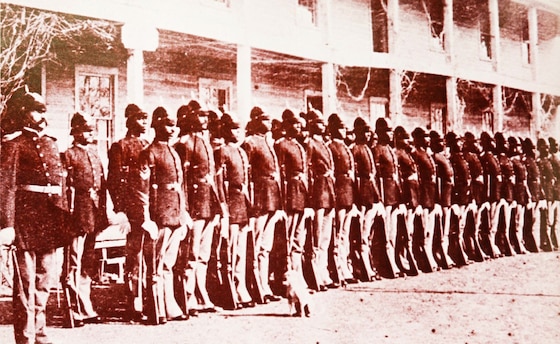 |
The Black Twenty-fifth Infantry Regiment stationed at Fort Randall until 1892.
|
The Niobrara chalk formation, deposited by a greatepeiric sea, runs from Cedar County, Nebraska, upstream nearly to the Great Bend of the Missouri. This chalk is the best foundation material available in the upper Missouri basin. There are some fracture joints and bentonite seams in the chalk, but at the Fort Randall damsite, the chalk is generally tight. It permits little seepage of water there, and this creates very little of the hydrostatic pressure which can cause misalignment of even huge structures.
The District decided to locate the dam's tunnels and outlet works on the left bank of the river because of the presence on the right bank of a chalk "island" covered with loess soil and cut by ravines filled with clays. On the left bank, the tunnels could be drilled through solid chalk, and less overburden needed to be removed. Early in 1948, a contractor's crew began to remove overburden from the site of the dam's powerhouse, approach channel, and outlet works and to place it in the embankment.
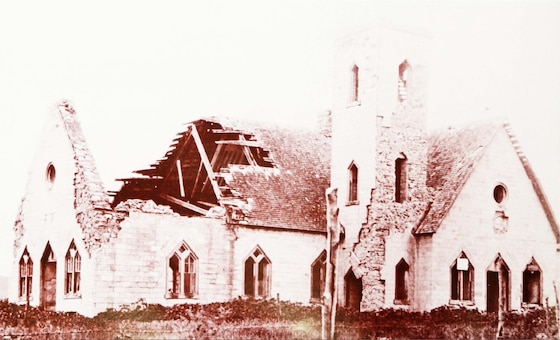 |
Christ Church, which was struck by lightning and a tornado
|
Heavy equipment accomplished the earthwork. Great draglines scooped out 8 cubic yards a bite from the borrow areas. The shovel filled each of the eleven 18-ton-capacity Mack trucks used on the job with just two such bites. The trucks dumped the earth on the embankment, and other equipment graded it down and sprinkled it with water. The sprinkling permitted the soil to be compacted to the desired density. Great sheepsfoot rollers ran back and forth over the fill, compressing it. A lighting system allowed the work to proceed at night through two 10-hour shifts, 6 days a week. At the height of construction, almost 5,000 people worked on the dam. Western Contracting Corporation of Sioux City did the majority of the excavation and earthfill work. When completed, the embankment measured 10,700 feet in length.
Western Contracting also employed the portable dredge Western Chief, designed and built for the project within 11 months by the Erickson Engineering Company of Tampa, Florida. The Western Chief was the most powerful suction dredge of the day. Capable of developing 10,950 horsepower, it carried 1,500 tons on a 36-inch draft and had hull dimensions of 170 by 46 by 11 feet. The Western Chief came to the launch site in 21 sections. These, when assembled, gave it 30 watertight compartments. Practically unsinkable, the Western Chief dredged to depths of 48 feet through soft or medium-hard rock.
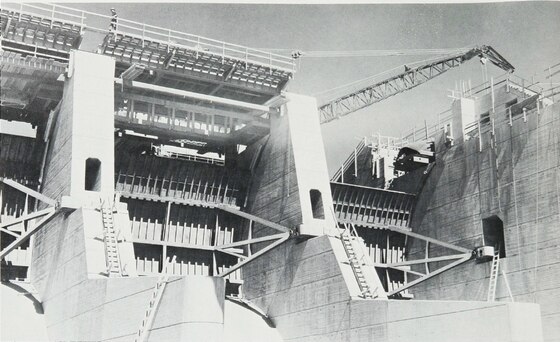 |
Bridge being constructed on top of spillway gates
|
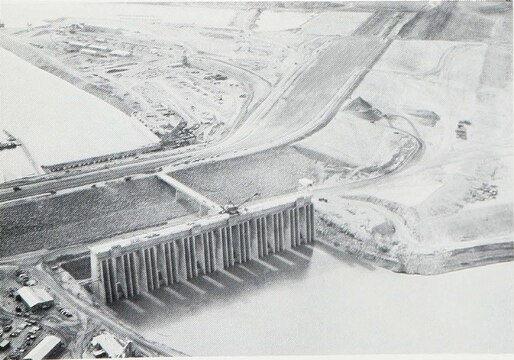 |
Completed intake structure |
The Western Chief went to work immediately upon its launching in April 1951. By the end of that year, it had dredged approximately 2.4 million cubic yards of material out of the approach channel and tailrace. The approach channel would directthe reservoir water to the power tunnels, and the tailrace would carry the water from the generators back to the river channel.
Beginning in May 1949, the Silas Mason Company of Shreveport drilled eight power-generating tunnels with 28-foot inside diameters through the chalk along with four 22-foot inside-diameter flood control tunnels. The tunnels were 875 feet long. The firm installed penstocks in the lower 648 feet of the power tunnels for the generation of electricity. A similar penstock was installed in one of the flood control tunnels so that it could be connected to a generator at a later date if desired.
Silas Mason began work on the first two tunnels using conventional line-drilling and blasting. The firm's project manager, R. B. Jewel, soon found a better method of boring the tunnels. He had a 9-foot conventional slabbing saw or coal saw mounted on a pair of great steel rings welded to a jumbo. He ran the saw into the chalk at the 4 o'clock position, had it cut its way on a circular arc to the 7 o'clock position, and then removed it. He cut back into the chalk a few inches farther around the circle, ran around the arc to 9 o'clock, and retracted it again until miners using jackhammers had drilled 41 blast holes 8 feet deep into the rock. Then he continued around the arc to within a few inches of his 4 o'clock starting point and removed the saw, leaving two plugs to hold the huge cylinder of chalk in place. Jewel found that two men operating the saw jumbo could cut as much circle periphery in 1.5 hours as could 16 men by line-drilling in 3 hours.
After the saw jumbo had been pulled out of the hole to work leapfrog fashion on an alternate tunnel, miners blasted out the cylinder of chalk. Mucking machines then moved in to load the trucks. These machines required 2 minutes to load one of the 10-cubic-yard mucking trucks, while it took the drivers 4 minutes to move one of the trucks out of the tunnel and another into position. All the while, two huge fans ventilated the tunnel. The saw jumbo was successful. In one recordsetting week, it cut through 331 feet in a 28-footdiameter tunnel. The jumbo saved money for the contractor because it reduced the normal 6-inch margin of overbreak in half, so that he did not have to blast an unneeded 3 or 4 inches of diameter. The District saved money because it did not have to pay a later contractor for 3 or 4 inches of extra concrete down the length of the 12 tunnels.
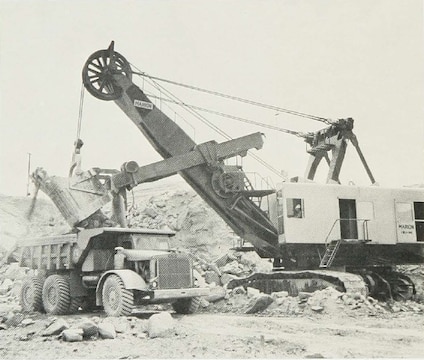 |
Marion 191-M shovel and Euclid dump
|
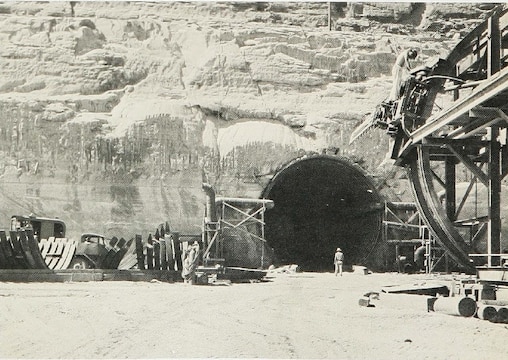 |
Coal saw being assembled |
Although work had begun on both the tunnels and the intake structure in 1949, Silas Mason had virtually completed the tunnels by the end of 1951 while work on the intake structure continued. The function of the intake structure was to control the flow of water through the 12 tunnels. It was comprised of 12 towers that measured 65 by 110 by 185 feet that stood together in close rank.
A joint venture of the AI Johnson Construction Company and the Winston Brothers Company, both of Minneapolis, built the intake structure under an $11.8 million contract. Its local batching plant mixed over 193,000 cubic yards of concrete-enough to lay 74 miles of two-lane highway. Charles Brown, the Chief of Construction on Omaha District's Fort Randall staff, made sure that the quality of the concrete was carefully controlled. District personnel tested the ingredients that went into the concrete before it was mixed and closely monitored the temperature of the aggregate. They tested it again when it was ready to be poured. By July 1952, the intake structure was ready to receive the Missouri.
The Omaha District then turned to the Western Chief to pump a 200,OOO-cubic-yard stockpile of select chalk into a temporary dam to close the Missouri's natural channel and divert its waters through the newly built intake structure and tunnels. This would be the first use of the hydraulic placement method of closure in such a large project. The dredge placed the base of the weir in late April and May while 50,000 to 70,000 cubic feet per second of water rushed over it. The weir itself was built in July, a month after the Missouri's spring crest had passed. Closure was attained at 1:10 p.m. on July 20, after 666,000 cubic yards of dredged material had been placed.
A year later, District employees observed that grooves were developing on the rollers and tracks of the 50-ton gates that regulated the flow of water through the intake structure. The grooves suggested that the gates vibrated while being operated. To test the gates and ascertain the seriousness of any vibration, the Omaha District called upon the U.S. Army Engineer Waterways Experiment Station in Vicksburg, Mississippi. That agency sent F, B. Campbell, Chief of its Hydraulic Analysis Branch, with a pickup truck of scientific gear to Fort Randall in January 1954 to test the gates. Campbell's research was the first ever conducted on gates of this type. Campbell welded an accelerometer to the gates and recorded their behavior on an oscillograph.His tests were then repeated at higher pool levels in September 1954 and August 1955. Waterways Experiment Station personnel concluded that no significant vibration was occurring.
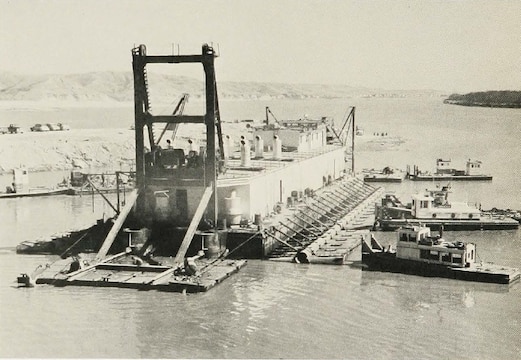 |
Moving Western Chief from Fort Randall
|
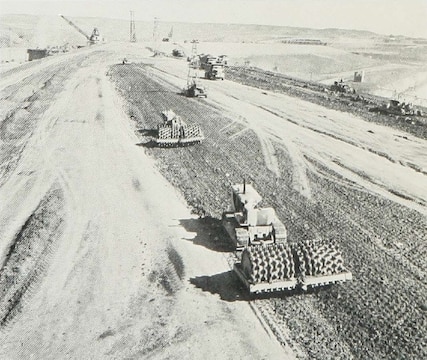 |
Sheepsfoot rollers on embankment |
Several firms joined to build the spillway and its Tainter gates and stilling basin. Excavation for these works, begun in 1951, was relatively simple as the foundation chalk could be cut easily in successive banks. The 1,OOO-foot-wide spillway required 500,000 cubic yards of concrete. The flow of water over the spillway was controlled by 21 Tainter gates, each 40 by 29 feet in size.
Oscar McCormick, superintendent at Fort Randall for a combine of Minneapolis and Omaha firms holding an $8.4 million spillway contract, developed a rig to drill holes for anchor bars in the spillway's chalk walls. The rig carried an air compressor on a Caterpillar-tracked platform and had a steel runner inclined above it. A drill moved up and down the runner sinking 8-inch-diameter holes 22 feet deep into the chalk at intervals of 8 feet. The drill bit had adjustable teeth which spread out at high speeds. When the bit neared the end of the hole, the drill operator increased its speed, reaming out an anchor bell. Workmen then ran steel anchor bars into the holes and poured grout into the anchor bells at the end of the holes. So grouted and set, the bars hold cement slabs tight against the chalk walls. The Omaha District concluded that this procedure saved $1 million and gave the District experience that it later used in constructing the North American Air Defense Command's Combat Operations Center under Cheyenne Mountain in Colorado.
Well under the Niobrara chalk, which is split in places by fracture joints and bentonite seams, lies the Codell aquifer. All across the Missouri River basin, hydrostatic pressure from the aquifer poses problems to builders. After the excavations for the chute and stilling basin were completed, Corps officials ordered 35 relief wells drilled to reduce the uplift capability of the aquifer and thus give the spillway structures more stability. Construction of the powerhouse and its generating equipment was a $35 million job. Four firms provided this work. Donovon-Lovering-Boyle built the powerhouse itself, which stood 710 feet long, 100 feet wide, and 150 feet high. Allis-Chalmers installed the eight turbines, Westinghouse Electric built the eight 40,OOO-kilowatt generators that those turbines would drive, and Pittsburgh-Des Moines Steel erected the eight penstocks and surge tanks.
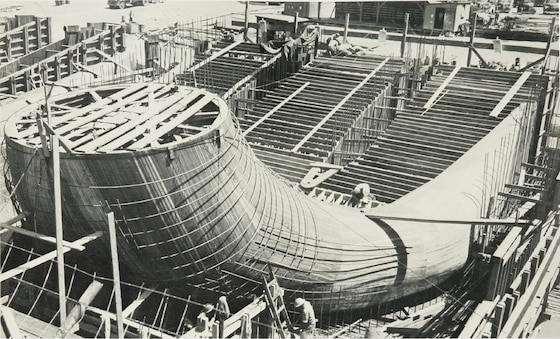 |
Powerhouse draft tube substructure
|
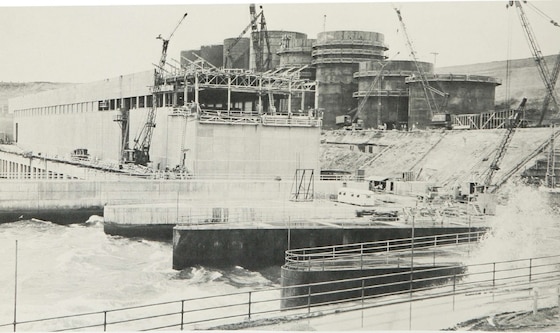 |
General view of powerhouse structure, 3 August 1954 |
Fort Randall's first power flowed on March 15, 1954, a day of ceremony for both Federal and State officials. President Eisenhower spoke over the radio from the White House to 600 people gathered in the Fort Randall powerhouse and then tapped a Western Union key to signal Governor Sigurd Anderson to start the generators. Anderson in turn spun the giant turbine, and the dam's first generator began producing electricity. Speeches followed. Omaha District Engineer Colonel Thomas Hayes III listened while former Governor George Michelson and Governor Anderson reminded the audience that South Dakota was sacrificing 500,000 acres of land for the main stem reservoirs. The South Dakotans expected benefits from Fort Randall Dam and the others as they were completed.
Only a small portion of those benefits accrued in 1954. On the day of the ceremony, the reservoir pool stood at an elevation of 1313 feet above mean sea level, well shy of the 1350-foot elevation needed to produce full power. That higher level could not be reached until the giant Oahe Dam was completed, because Fort Randall Dam had to maintain a flood control capacity of 3.5 million acre-feet until then.
The eighth and last of Fort Randall's generators began operation on 10 January 1956. The Bureau of Reclamation marketed the power produced by the project, using both its own transmission lines and private lines. The dam provided power north to Fort Thompson where Big Bend Dam would be built and south to Grand Island and Columbus, Nebraska. By 30 June 1956, the Omaha District Engineer could report that the Fort Randall Project was 99 percent complete at a total cost of $183 million. This figure was almost 2.5 times as large as the original cost estimate. Within the previous 12 months, the dam's generators had produced more than 1 billion kilowatt-hours of electricity. By the early 1970's, the dam was producing over 2 billion kilowatt-hours of electric power annually. 